Sunday, July 22, 2018
Coefficient of performance ( COP )
A mechanical engineer specializes in HVAC (heating, ventilation, and air conditioning) designs, develops, and maintains systems that control the temperature, humidity, and overall air quality in buildings. This includes selecting, sizing, and specifying HVAC equipment and controls, analyzing energy consumption and efficiency, and troubleshooting and resolving HVAC-related issues. They may also be involved in commissioning new HVAC systems, performing routine maintenance, and providing guidance to other members of a building's design or construction team.
Fan Coil Unit F.C.U
Fan Coil Unit Systems. A fan coil unit(FCU) contains a fan which draws the air in a space into the unit then blows it over a cooling or heating coil. The air comes out of the FCU either cooler or hotter than before.
A mechanical engineer specializes in HVAC (heating, ventilation, and air conditioning) designs, develops, and maintains systems that control the temperature, humidity, and overall air quality in buildings. This includes selecting, sizing, and specifying HVAC equipment and controls, analyzing energy consumption and efficiency, and troubleshooting and resolving HVAC-related issues. They may also be involved in commissioning new HVAC systems, performing routine maintenance, and providing guidance to other members of a building's design or construction team.
WORKING PRINCIPLE OF AN AHU
Air Handling unit or AHU is an assembly of air conditioning components (such as fans, cooling coils, filters, humidifiers and dampers) integrated into a self-contained package and installed as a single unit, which is connected to system of metal duct work that distributes the conditioned air.
We difference two types of AHU :
- simple flow: the AHU whether works in 100% fresh air, or air intake, or works with the two of them.
- dual flow: the AHU is working with the most optimal configuration, by chosing between quantity of fresh air, total treated air, air intake, return air, according to the situation.
How does a simple flow AHU work ?
It is actually very easy to understand : the AHU pumps the designed external air, which will be treated in temperature and humidity, as well as quality of composition with different type of filters. This treated air will be carried to respective areas by means of ducting.
For a dual flows AHU, besides the first objective explained previously, the AHU will extract the air from the areas that can’t be recycled back in the AHU (air too polluted or areas which requires a percentage of extracted air), and will be rejected out of the structure.
Objectives of the AHU :
- Fresh air intake (which replaces the air polluted)
- Air treatment (by filtration)
- Humidity and temperature control of the air supply
- Structure easy to install in each type of architectural configuration
- Minimal surface facilities required (specification important due to the m² price today).
- Noise reduction (no need to open any windows)
- Integrated regulation with an software adapted to health services
- Plug and Play unit.
- Reduction of the ductwork and installation – Important saving of time and money..
The AHU provide pre cooling (pre heating) of the ventilation air and thus take care of only a relative small part of the cooling (heating) load. In addition the energy for pre cooling (pre heating) does not come from the AHU itself, but is provided by an external source, such as a chiller (boiler or furnace).
Some AHUs like dual stream VMC are working with exchanges boxes for effecting heat energy recovery, thanks to the use of the heating recovered to heat up the air intake.
The dual flows AHUs know how to work according to different working systems.
The different types of filtration:
- Total recycling : no fresh air is brought, air traitment is working as closed circuit, only with the ambient air,
- Partial rcycling : part of the air treated is rejected and replaced by fresh air.
- 100% Fresh air : the air intake flow equals to the air supplied. It becomes therefore interesting to retrieve the energy brought by a heat recovery unit on the air intake “polluted”.
A mechanical engineer specializes in HVAC (heating, ventilation, and air conditioning) designs, develops, and maintains systems that control the temperature, humidity, and overall air quality in buildings. This includes selecting, sizing, and specifying HVAC equipment and controls, analyzing energy consumption and efficiency, and troubleshooting and resolving HVAC-related issues. They may also be involved in commissioning new HVAC systems, performing routine maintenance, and providing guidance to other members of a building's design or construction team.
AHU introduction
An Air Handling Unit (AHU) is used to condition and circulate air as part of a heating, ventilating, and air-conditioning system. The basic function of the AHU is take in outside air, condition it and supply fresh air to a building. All exhaust air is discharged, which secures an acceptable indoor air quality.
A mechanical engineer specializes in HVAC (heating, ventilation, and air conditioning) designs, develops, and maintains systems that control the temperature, humidity, and overall air quality in buildings. This includes selecting, sizing, and specifying HVAC equipment and controls, analyzing energy consumption and efficiency, and troubleshooting and resolving HVAC-related issues. They may also be involved in commissioning new HVAC systems, performing routine maintenance, and providing guidance to other members of a building's design or construction team.
Saturday, July 21, 2018
Basic Refrigeration Cycle
Basic Refrigeration Cycle
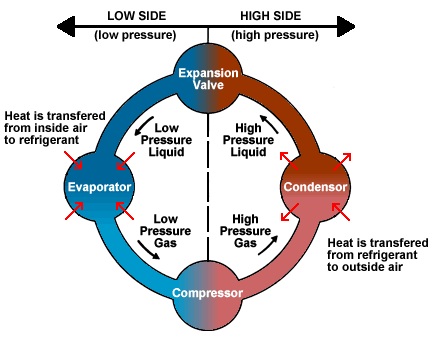
Principles of Refrigeration
- Liquids absorb heat when changed from liquid to gas
- Gases give off heat when changed from gas to liquid.
For an air conditioning system to operate with economy, the refrigerant must be used repeatedly. For this reason, all air conditioners use the same cycle of compression, condensation, expansion, and evaporation in a closed circuit. The same refrigerant is used to move the heat from one area, to cool this area, and to expel this heat in another area.
- The refrigerant comes into the compressor as a low-pressure gas, it is compressed and then moves out of the compressor as a high-pressure gas.
- The gas then flows to the condenser. Here the gas condenses to a liquid, and gives off its heat to the outside air.
- The liquid then moves to the expansion valve under high pressure. This valve restricts the flow of the fluid, and lowers its pressure as it leaves the expansion valve.
- The low-pressure liquid then moves to the evaporator, where heat from the inside air is absorbed and changes it from a liquid to a gas.
- As a hot low-pressure gas, the refrigerant moves to the compressor where the entire cycle is repeated.
Note that the four-part cycle is divided at the center into a high side and a low side This refers to the pressures of the refrigerant in each side of the system
A mechanical engineer specializes in HVAC (heating, ventilation, and air conditioning) designs, develops, and maintains systems that control the temperature, humidity, and overall air quality in buildings. This includes selecting, sizing, and specifying HVAC equipment and controls, analyzing energy consumption and efficiency, and troubleshooting and resolving HVAC-related issues. They may also be involved in commissioning new HVAC systems, performing routine maintenance, and providing guidance to other members of a building's design or construction team.
How does #chiller work #Imran
Chiller System Overview
Chillers use either a vapor-compression or absorption refrigerant cycle to cool a fluid for heat transfer. Both chiller types rely on three basic principles.
- First - When a liquid is heated it vaporizes into a gas, and when a gas is cooled it condenses into a liquid
- Second - Lowering the pressure above a liquid reduces its boiling point and increasing the pressure raises it
- Third - Heat always flows from hot to cold.
Basic Cooling Cycle
The basic cooling cycle is the same for both vapor-compression and absorption chillers. Both systems utilize a liquid refrigerant that changes phase to a gas within an evaporator which absorbs heat from the water to be cooled.
The refrigerant gas is then compressed to a higher pressure by a compressor or a generator, converted back into a liquid by rejecting heat through a condenser and then expanded to a low- pressure mixture of liquid and vapor that goes back to the evaporator section. The cycle is repeated.
Vapor Compressor Chiller

A vapor-compression chiller consists of four primary components of the vapor-compression refrigeration cycle. They include a compressor, evaporator, condenser and a metering device.
Vapor-compression chillers typically utilize HCFC or CFC refrigerants to achieve a refrigeration effect. Compressors are the driving force in a vapor-compression chiller and act as a pump for the refrigerant.
Compressed refrigerant gas is sent from the compressor to a condenser unit that rejects the heat energy from the refrigerant to cooling water or air outside of the system.
The transfer of heat allows the refrigerant gas to condense into a liquid which is then sent to a metering device.
The metering device restricts the flow of liquid refrigerant which causes a drop in pressure. The drop in pressure causes the warm refrigerant liquid to change phase from liquid to gas and in doing so absorbs heat from the water to be cooled due to adiabatic flash evaporation.
The metering device is positioned so that the expanding refrigerant gas is contained within the evaporator, transferring the heat energy from the water to be cooled into the refrigerant gas. The warm refrigerant gas is then sent back to the compressor to start the cycle over again and the newly chilled water in the separate loop can now be used for cooling.
Absorption Chiller

An absorption chiller uses a heat source to drive the refrigeration cycle in place of a mechanical compressor. Absorption chillers utilize two fluids which include a refrigerant, typically water and an absorbent, typically a lithium bromide solution or ammonia.
These liquids are separated and recombined in the absorption cycle where due to the low pressure conditions the water can more easily change phase than it normally would, and the high affinity of the two liquids promotes easy absorption.
The cycle begins with a mixture of liquid refrigerant water and absorbent that is heated at a higher pressure to boil the water out of solution. The refrigerant water vapor is then sent past a condenser coil where heat rejected and it is condensed into a high pressure liquid. The liquid refrigerant water is then sent to the lower pressure evaporator where throughadiabatic flash evaporation returns to a gas, absorbing the heat from the water to be chilled. The concentrated liquid absorbent from the generator is sent back to be recombined with the low-pressure refrigerant vapors returning from the evaporator starting the cycle over again.
A mechanical engineer specializes in HVAC (heating, ventilation, and air conditioning) designs, develops, and maintains systems that control the temperature, humidity, and overall air quality in buildings. This includes selecting, sizing, and specifying HVAC equipment and controls, analyzing energy consumption and efficiency, and troubleshooting and resolving HVAC-related issues. They may also be involved in commissioning new HVAC systems, performing routine maintenance, and providing guidance to other members of a building's design or construction team.
Friday, July 20, 2018
What does TR mean in air conditioning
What does TR mean in air conditioning
Originally 1 TR was defined as the rate of heat transfer required to make 1 short ton (2000 lbs) of ice per day from water at 0oC. American Society of Heating, Refrigerating and Airconditioning Engineers (ASHRAE) defines 1 TR as equivalent to a refrigeration capacity of 3516.85 W or 3023.95 kcal/h.
.
A mechanical engineer specializes in HVAC (heating, ventilation, and air conditioning) designs, develops, and maintains systems that control the temperature, humidity, and overall air quality in buildings. This includes selecting, sizing, and specifying HVAC equipment and controls, analyzing energy consumption and efficiency, and troubleshooting and resolving HVAC-related issues. They may also be involved in commissioning new HVAC systems, performing routine maintenance, and providing guidance to other members of a building's design or construction team.
Superheat and Subcooling
Superheat and Subcooling
Superheat and subcooling are critical to the refrigeration cycle, but can be tough concepts to visualize.
Let’s start with superheat:
Boiling is when a liquid gains heat and transforms into a vapor.
Superheat occurs when that vapor is heated above its boiling point.
Let’s say that refrigerant boils at 40 degrees at a low pressure in the evaporator. The vaporized refrigerant is continuously heated, elevating its temperature to become a 50-degree vapor. This increase in temperatureabovethe boiling point is known as superheat. The formula to calculate superheat uses the current temperature and boiling point.

In this example, the superheat is 10-degrees.
Superheat is critical in HVAC because it ensures the liquid refrigerant is boiled off before it leaves the evaporator and heads to the compressor. Even small amounts of liquid can cause detrimental damage to the compressor in an HVAC system.
While evaporation and superheat occur in the evaporator, condensation and subcooling occur in the condenser.

Condensation is when a vapor loses heat and turns into a liquid, butsubcooling is when that liquid is cooled below the temperature at which it turns into a liquid.
Let’s use the same refrigerant with a high pressure boiling point of 120 degrees for the following example:
The refrigerant is a 140 degree vapor heading into the condenser. Once the condenser cools the refrigerant to 120 degrees, it will begin to turn back into a liquid. But the cooling does not stop there! Subcooling is also calculated using the boiling point (sometimes referred to as the condensing point) and current temperature.

So, if the condenser brings the refrigerant temperature down to 105 degrees, it has been subcooled by 15 degrees. In the refrigeration cycle, subcooling is an important process that ensures liquidrefrigerant enters the expansion device.
Key takeaways: superheat occurs in the evaporator to protect the compressor, and subcooling occurs in the condenser to protect the expansion device
A mechanical engineer specializes in HVAC (heating, ventilation, and air conditioning) designs, develops, and maintains systems that control the temperature, humidity, and overall air quality in buildings. This includes selecting, sizing, and specifying HVAC equipment and controls, analyzing energy consumption and efficiency, and troubleshooting and resolving HVAC-related issues. They may also be involved in commissioning new HVAC systems, performing routine maintenance, and providing guidance to other members of a building's design or construction team.
HVAC Basic
HVAC Basics
Facility maintenance managers, HVAC contractors; HOA board members; estate and high-rise building managers; building and facility engineers; and commercial property managers all have one important responsibility to think about - running an HVAC.
Heating, cooling and air conditioning is vital to any part of real estate, whether for residential, commercial or industrial purposes.
Here's a list of HVAC system fundamentals:
What is HVAC?
Heating, Ventilation and Air Conditioning systems are tasked with circulating fresh air within living spaces, while maintaining the optimal temperature to keep the occupants comfortable. Maintaining an efficient, working HVAC system is paramount to keeping management smooth and providing thermal comfort.
Parts of an HVAC System
Property managers should have an idea of how an HVAC system operates and what to do when complications occur. Here are the most important things to remember about each part:
Compressor
The heart of an HVAC system, compressors pump the refrigerant through respective components in a looping pattern. The refrigerant enters the compressor as low-pressure vapor and exits as high-pressure vapor.
Condenser Coil
This HVAC system component is responsible for rejecting the heat load absorbed by the evaporator coil. If the condenser oil is neglected, improper cooling will occur causing a high head pressure.
Evaporator Coil
This component absorbs the heat load to the condenser coil for eventual rejection. If the evaporator coil is impacted or dirty, then the HVAC will have improper cooling and low suction pressure.
Condenser Fan Motor
Condenser fan motors help in rejecting the heat load and maintaining optimal head pressure for optimal compressor operation.
Evaporator Blower Motor
Evaporator blower motor is designed to force or push manipulated air through the duct stream.
Thermostatic Expansion Valve
The TXV is a device that regulates the amount of liquid refrigerant flowing through the evaporator. It is designed to maximize evaporator efficiency while diverting the flow of excess refrigerant back into the compressor (called floodback).
Cooling Tower
A component of an HVAC system which rejects the heat load absorbed by either the heat pump or evaporator coil carried by water. The water in it transports the heat load which was absorbed by the evaporator coil, dissipating it in the cooling tower. The water that passes via the heat exchanger normalizes head pressure.
Chiller
This is a machine that provides chilled water, which is used in conjunction with the HVAC system's cooling.
Pumps
These components are primarily designed to move water at the chill water and condenser water supply sections. Pumps move water chilled to 44 degrees to fancoils, and once the water reaches the fancoil, temperature rises to roughly around 47-52 degrees. Pumps that move the condenser water supply are rejected at cooling temperatures ranging from 90 to 100 degrees. Factors such as demand load, ambience, the cooling tower fill's condition, and strainers can vary the temperature during circulation.
Duct System
This can either be rectangular or spiral, flanged or drive. The main trunk line is where the main HVAC air flows, branching out to distribution points that carry the cooled or warmed air into small office suites and large conference rooms in commercial buildings.
Boiler
The boiler is pressure equipment which heats water. The choices when it comes to selecting boiler types are either low or high pressure systems, or hot water and steam.
Energy Management Monitoring Systems
Also known as BAS (Building Automation Systems), this HVAC component helps schedule, control and monitor commercial equipment such as cooling towers, pumps, package units, air compressors and handlers, boilers, temperature sensors, chillers and VAV boxes within the office and in office living spaces.
A mechanical engineer specializes in HVAC (heating, ventilation, and air conditioning) designs, develops, and maintains systems that control the temperature, humidity, and overall air quality in buildings. This includes selecting, sizing, and specifying HVAC equipment and controls, analyzing energy consumption and efficiency, and troubleshooting and resolving HVAC-related issues. They may also be involved in commissioning new HVAC systems, performing routine maintenance, and providing guidance to other members of a building's design or construction team.
Subscribe to:
Posts (Atom)
-
Determining Duct Air Flow in CFM using to Pressure Sensor by Imran To calculate Air Flow in Cubic Feet per Minute (CFM), determine the Fl...
-
Superheat and Subcooling Superheat and subcooling are critical to the refrigeration cycle, but can be tough concepts to visualize. Le...
-
06EF299610 Semi Hermetic Compressor by Mohammad Imran. High-flow, automatically reversi...